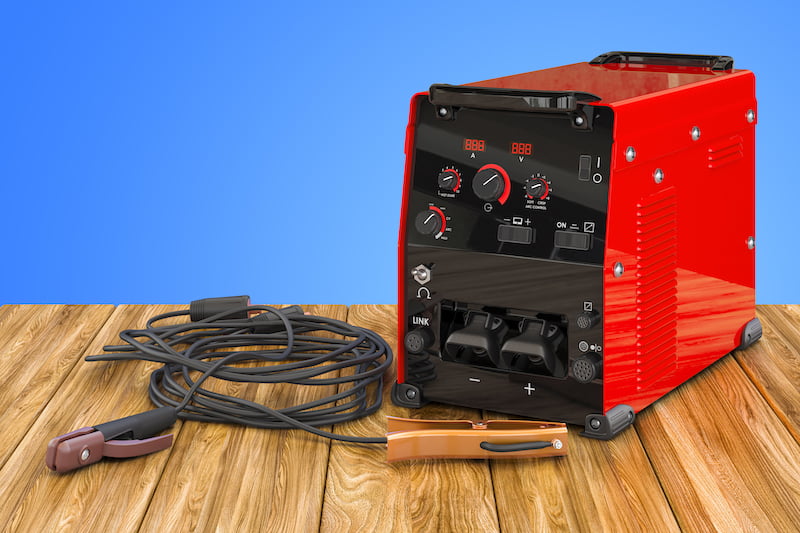
Welding has been seen as one of the most important steps in industries across various sectors. The type of current that is being used in the welding process, whether it be AC (alternating current) or DC (direct current), can have a huge impact on the overall welding process.
It is a crucial step in the manufacture of metal, and for best results, the appropriate tools must be used. Selecting between an AC or DC welding machine is one of the most important choices you’ll have to make. Let’s examine the distinctions between these two welding techniques that are most widely used.
Navigation
- Introduction to AC Welding
- Introduction to DC Welding
- Difference Between AC and DC Welding
- AC Welding Overview
- DC Welding Overview
- Conclusion
Introduction to AC Welding
AC welding utilizes an alternating current throughout its welding process. The AC welding’s unique property is that it produces a current that alternates between the positive and negative cycles. This alternating process gives us a cleaner weld and a deeper stronger weld.
The AC welding process is the best option for you if you are looking to work with non-ferrous metals such as aluminum.
In comparison, the other most popular welding process is the DC welding process. And in comparison to DC welding AC welding machines offer several advantages. AC welding machines are the best option if you are planning on working with aluminum and other non-ferrous metals. AC machines are a fantastic option for thicker textiles since they offer a greater depth of penetration. They are also easier for novices to use since they are more accommodating to variations in the welding angle.

Introduction to DC Welding
In contrast, DC welding forms an arc between the electrode and the workpiece using direct current. Only one direction of current flow results in a more stable arc and improved control over the welding process. You will find that the majority of welding machines are in DC.
DC welding is a very popular method for joining ferrous and other steel metals.
DC welding equipment offers its own unique set of benefits. One of these benefits is that DC welding offers more improved control over the entire welding process. The steady arc that DC machines produce makes it easier for the user to manage the weld puddle and be able to produce precise welds. In addition to being more energy-efficient than AC machines, DC machines also require less power to generate the same amount of heat.
Difference Between AC and DC Welding
A crucial step in manufacturing and construction, welding joins materials together using a variety of methods. Direct current (DC) and alternating current (AC) welding stand out among these methods for their unique uses and benefits. Budding welders must comprehend the numerous distinctions between AC and DC welding so that they can choose the appropriate technique for a given operation.

It is important to note that AC and DC are not the only factors to consider when selecting a welding machine. There are several different types of welding, the main three being Stick, MIG, and TIG. You can read about them here.
Alternating Current (AC) Welding
Current Flow
The direction of AC periodically changes. Normally, the electrons flow at a frequency of 60 Hz in the United States (50 Hz in certain countries) and then swap back and forth in either direction. This indicates to us that the current changes 60 times per second, flip-flopping from positive back to negative in rapid succession.
Features of AC Welding
- Arc Stability: Because the arc extinguishes and re-ignites with every cycle of the current, AC welding might be seen as less stable than DC welding.
- Deep Penetration: One of AC’s main advantages is its ability to work with thick materials.
- Magnetic Arc Blow: AC is helpful for welding in difficult locations or on magnetized materials because it lessens the phenomenon known as magnetic arc blow, in which the arc is deflected by magnetic fields within the workpiece.

Applications of AC Welding
- Aluminum Welding: Because AC has a cleaning action that eliminates the oxide layer from the metal surface, it is frequently utilized for welding magnesium and aluminum.
- High-Frequency Stabilization: when working on non-ferrous metals, such as aluminum and magnesium, high-frequency alternating currents are used to steady the arc.
- General Maintenance: Suitable for work on materials with different thicknesses for general maintenance and repairs.
Equipment
- Transformers: A transformer is needed for AC welding to reduce the high power supply voltage to a welding-safe level.
- Less Expensive: In comparison to DC welding equipment, AC welding equipment is typically simpler and less costly.
Direct Current (DC) Welding
Current Flow
DC currents flow in a single direction, providing a constant polarity. The direction can be either positive (DC+) or negative (DC-).
DC+ (Direct Current Electrode Positive, DCEP): The electrode is positive, and the workpiece is negative. Deeper penetration is achieved when utilizing this setup.
DC- (Direct Current Electrode Negative, DCEN): The electrode is negative, and the workpiece is positive. This setup provides a faster deposition rate and is useful for thin materials.
Features of DC Welding
- Arc Stability: The smoother the welding process, the more stable and flicker-free arc that DC welding produces.
- Penetration and Deposition: DC- offers a higher deposition rate with less penetration, whilst DC+ offers deeper penetration.
- Improved Control: This enables more accurate and reliable welds.
- Less Spatter: DC welding usually results in less spatter, which means cleaner welds and less clean-up after the weld.

Applications of DC Welding
- Steel and Ferrous Metals: DC welding is commonly used for welding steel and other ferrous metals.
- TIG Welding: DC welding is preferred by most of the industry specialists for TIG (Tungsten Inert Gas).
- Arc Welding: Arc welding is widely used in SMAW (Shielded Metal Arc Welding) and MIG (Metal Inert Gas).
- Thin Materials: DCEN is suitable when a person is welding thin materials. This is because of its high deposition rate and low penetration rates.
Equipment
- Rectifiers: DC welding machines use rectifiers that convert AC from the power source to DC which is suitable for welding.
- Inverters: Modern DC welding machines often use inverter technologies. These are much more efficient, highly portable, and provide better control over the overall welding parameters.
Conclusion
Each type of welding—AC and DC—has special benefits and uses. Depending on the materials that are being welded and the desired results, one might have to choose between AC and DC welding.

- Arc Stability: DC machines offer better arc stability compared to AC. This results in smoother and more controlled welds.
- Weld Quality: DC machines are often favored for their ability to produce high-quality welds with minimal defects.
- Versatility: DC machines are more versatile and can be used for a wider range of welding tasks. Whereas AC welding machines have specific applications for certain materials.
- Penetration: AC machines are better suited for materials like aluminum and magnesium.
The particulars of the project are what usually determine the type of welding process that will be used. By being knowledgeable of the above variations, welders can choose the right current type, which will guarantee the best performance and outcomes for their particular welding jobs.