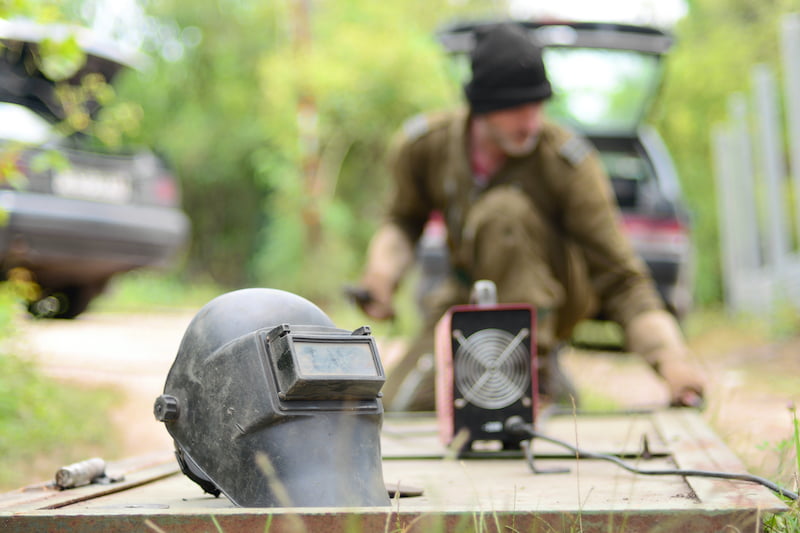
Welding is a very common skill used for construction, automotive repair, and more. The process consists of joining materials or metals with the help of high heat. Welding is essential for creating strong structures.
Today we will look at the top three most common welding types: Stick welding, MIG welding, and TIG welding. The common techniques we will discuss have advantages and are suitable for different tasks. Once you get a grasp of these welding types, you can go ahead and select the right one for your work.
No matter if you’ve just started learning the basics, this article will help you get to know everything regarding welding techniques.
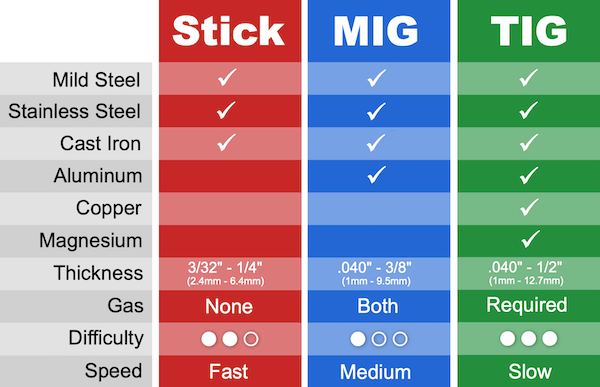
Navigation
Stick Welding: What is it?
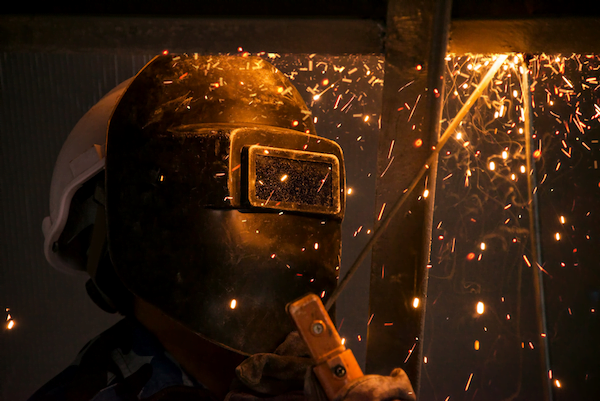
Stick welding is a manual arc welding process that is very simple to execute. This welding process starts with a consumable, which is also referred to as a stick, and is coated in flux.
Once you start the welding machine, an electric arc starts to form between the electrode and the base material. This arc generates intense heat that causes both the electrode and the base material to start melting and form a weld pool. Once the electrode melts, you will find the flux coating disintegrating. This will release a shielding gas and form a layer of slag.
Stick welding is highly effective due to the dual protection system of shielding gas and slag. You can use it easily in outdoor settings where wind can compromise the weld. Stick welding types can produce strong and reliable welds under less-than-ideal conditions. Read more about stick welding here.
Tools Used in Stick Welding
Stick welding is done with the help of the below tools.
- Welding Machine: provides the required electric current for the welding process.
- Electrodes: consumable rods coated in flux.
- Electrode Holder: used to clamp the electrode.
- Ground Clamp: helps to complete the electrical circuit.
- Protective Gear: primarily includes a welding helmet and protection gloves.
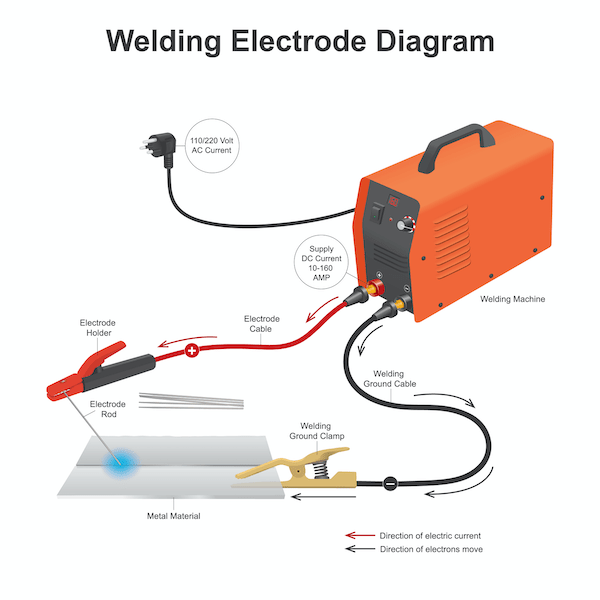
Benefits of Doing Stick Welding
Being the most effective, stick welding has many benefits over other welding types. Let’s check them out.
- Versatile: Stick welding can easily be done on any metal, like cast iron, steel, or stainless steel.
- Portable: All the tools used in stick welding can be taken anywhere on a two-wheeler itself. This makes it effective in situations where you have to pass narrow streets.
- Reasonable Price: As it requires less expensive tools, the overall cost of this welding is also reduced for the customers.
- Robust Technique: Because it can work pretty well in bad conditions too, like strong winds or dirty places, this is highly effective.
Use Cases for Stick Welding
As it is used in any working condition, most industries prefer stick welding over other techniques. Here are the industries that use stick welding daily.
- Construction Industry: Stick welding is good for structural work due to its strong, durable welds.
- Maintenance and Repair Industry: Stick welding has a good hold for repairing heavy machinery and tools.
- Industrial Fabrication: You will also find stick welding happening in the manufacturing of industrial components.
Great Tips for Stick Welding
Those who want to practice stick welding can use the below-mentioned advice for good-quality welds.
- Selecting the Electrode: You need to choose the right electrode for the material you need to weld.
- Correct Current and Voltage Setting: You need to adjust the welding machine so that the correct number of current passes in the electrode.
- Arc Length is Important: A great welder will always try to maintain a consistent arc length. This is usually the diameter of the electrode.
- Welding Speed: Try to move the electrode at a fixed speed so that there’s a uniform weld happening on the material.
MIG Welding: Get to Know it
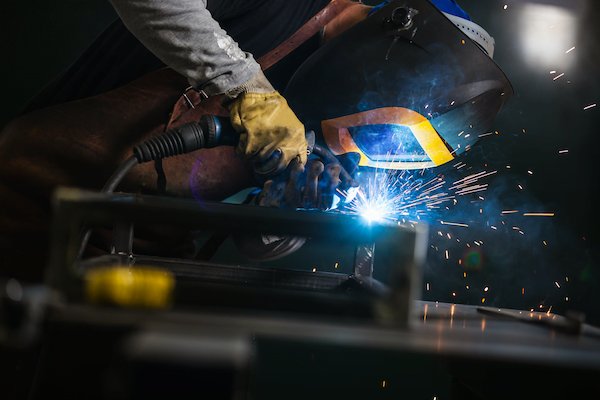
MIG welding is one of the most popular welding types, having a continuous wire feed as an electrode and an inert gas to protect the weld pool from contamination.
During the welding process, a wire electrode is fed through a welding gun. It starts melting when it comes into contact with the metal to create a clean weld.
The inert gas which is used in the MIG welding technique is argon or a mix of argon and carbon dioxide. This helps to protect the weld from other gases and finally get a perfect weld. Read more about MIG welding here.
Tools Used for MIG Welding
Welders use the below-mentioned tools for the MIG welding technique.
- Welding Machine: used to provide the required amount of electric current.
- Wire Feeder: continuously feed the wire electrode via the welding gun.
- Welding Gun: helps to direct the wire electrode and shielding gas to the weld pool.
- Shielding Gas Supply: will either contain argon alone or a mixture of argon and carbon dioxide.
- Protective Gear: these will include a welding helmet, protection gloves, and respiratory protection.
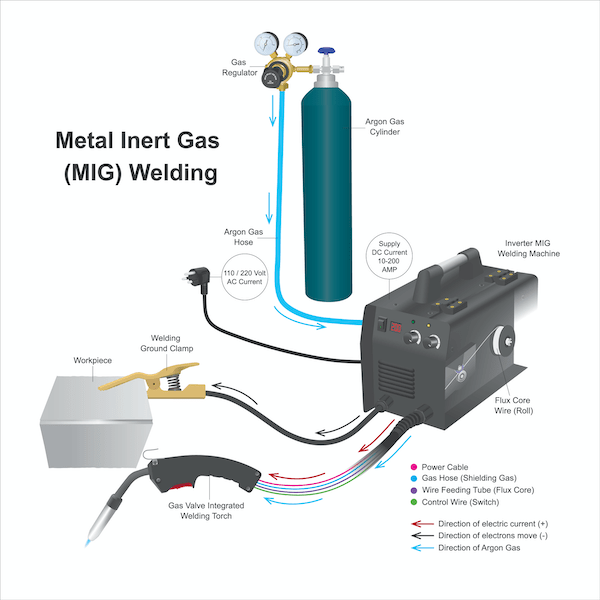
Benefits of Doing MIG Welding
MIG welding has many benefits over any other welding type. Let’s check them out one by one.
- Simple to Use: As there is a continuous wire feed, this makes MIG welding pretty straightforward. Even beginners can give it a shot after a few hours of practice.
- Faster speed: MIG welding is faster than the other welding techniques. This is a huge plus for performing tasks at large, time-sensitive projects.
- Support for All Metals: It is a suitable welding type for all types of heavy metals like steel, aluminum, or stainless steel.
- Perfect and Clean Welds: Because it has minimal spatter there is no need for post-weld cleanup.
Use Cases of MIG Welding
Because of its higher speed, it is used in big industries. Let’s check them out.
- Automotive Industry: It is used to either repair or manufacture car parts worldwide.
- Construction Industry: Big reality projects often use MIG welding to build strong frameworks for buildings.
- Manufacturing: MIG welding is also heavily used in the machinery and equipment processes. Its ability to handle various thicknesses of materials makes it one of the most commonly used welding types.
- Art and Sculpture: This is used by artists to create metal sculptures and art pieces.
Important Tips for MIG Welding
Welders who want to get a clean weld should follow the below welding techniques.
- A Proper Setup: Welders should know that the welding machine is set at the required voltage. Another important thing is to maintain the wire feed speed for the material being welded.
- Keep Proper Angle and Distance: An excellent welder will always keep a consistent angle and distance between the welding gun and the metal.
- Consistent Speed: Try to closely move the welding gun at a steady speed so that the weld is uniform at all places.
- Keep Practicing: Performing hours of welding will help to improve control and better welds.
TIG Welding: How it works
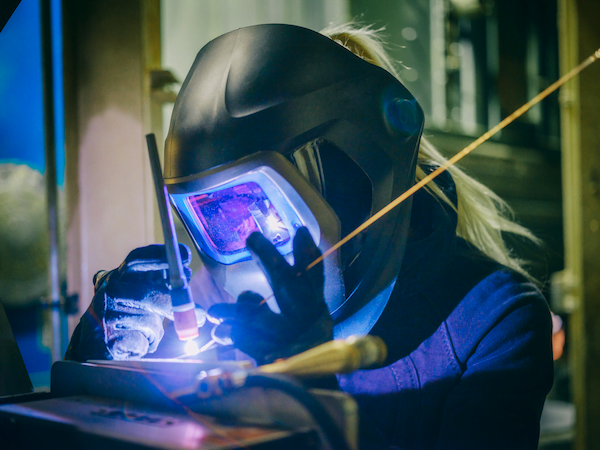
It is one of the most precise and high-quality welding techniques. TIG welding is also called Tungsten Inert Gas welding. This process uses a non-consumable tungsten electrode to produce the weld.
The electrode creates an electric arc between itself and the metal that needs welding. This produces heat so that the metal starts melting.
Argon is the inert gas used to protect the weld area from any air contamination. TIG welding gives clean and high-quality welds over other welding types. Read more about TIG welding here.
Tools Used in TIG Welding
- Welding Machine: will provide the amount of electric current required for welding.
- Tungsten Electrode: a non-consumable rod that generates the arc.
- Welding Torch: helps hold the tungsten electrode and direct the shielding gas.
- Shielding Gas Supply: argon gas is the main choice to protect the weld area.
- Filler Rod: it is helpful to add material to the weld but is optional.
- Protective Gear: these will include a welding helmet, protection gloves, and respiratory protection.

Benefits of Performing TIG Welding
You can check out the below benefits of TIG welding over other welding types.
- Highly precise: It will give you the best quality welding over all other welding types available in the market.
- Very Strong Welds: The welds generated with TIG welding are very strong and are considered unbreakable.
- Used for all metals: You can use it on metals such as stainless steel, aluminum, or copper.
- High control: This is one of the welding techniques that has excellent control over heat and filler material.
Use Cases of TIG Welding
Let’s check out the various industries where this type of welding is used.
- Aerospace Industry: It contains welding components that require high strength in the air.
- Automotive Industry: TIG welding helps to weld the most critical parts for new machinery and custom modifications for repairs.
- Medical Devices: It is used for manufacturing precise and reliable medical devices.
Best Tips for TIG Welding
Here, you will get to know all the tips and tricks to make the most of this welding technique.
- Electrode Selection: It’s very important to use the right tungsten electrode based on the material and thickness of the metal.
- Torch Angle and Distance: To maintain a consistent torch angle and distance from the metal you are welding.
- Puddle Control: Carefully control the weld puddle and add filler material as required.
Safety Precautions
- Always wear a welding helmet, hand gloves, and protective clothing. This will help you protect yourself from sparks and UV radiation.
- Perform the welding at a place that has proper ventilation to avoid inhaling harmful fumes during the welding process.
- Keep a fire extinguisher nearby in case of an emergency.
Conclusion: Top 3 Welding Types
Now we have understood the top three welding types, namely Stick, MIG, and TIG welding. Each of the welding types offers unique benefits for the users.
Stick welding is known for its simplicity and durability. It handles rusty or dirty surfaces well, and the tools are also portable.
MIG welding is considered for its speed and ease of use. This method is excellent for beginners and large-scale production. It produces clean, strong welds on a variety of materials.
TIG welding stands out for its precision and high-quality results. This technique is ideal for detailed and delicate work, such as in the aerospace and automotive industries. Understanding when and how to use each welding method is important.